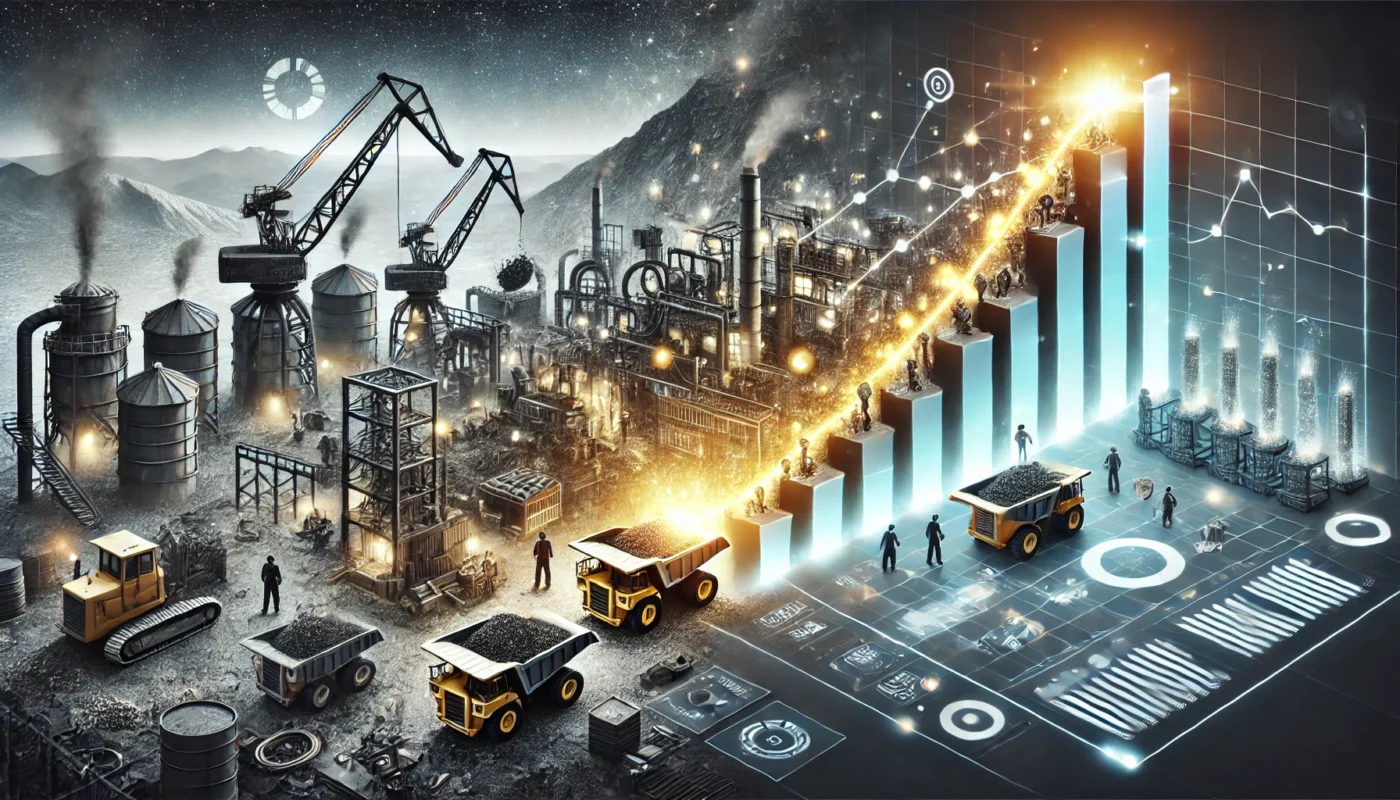
The Mining Industry’s Production Crisis
According to Dr. Bernd Elser, Accenture’s Global Lead for Natural Resources, mining companies have fallen short of their production targets by 2.6% annually over the past five years, resulting in a staggering $67 billion in lost revenue. Australian miners have been the worst performers in this regard.
Missing forecasted production is not an exception
The Impact of Missed Production Targets
The consequences of missing production targets are far-reaching. It not only erodes investor confidence but also leads to lost output and profits year after year. This, in turn, affects cash flow and market valuations, hindering growth and stifling opportunities for increased mining production. The issue of unpredictable production affects not only operational performance but also long-term planning and efficiency.
How can Mining Companies Get Back on Track?
To overcome these challenges, mining companies must embark on a structured transformation. This involves revamping their planning processes, asset management systems, and supply chain strategies. It requires developing new capabilities, reshaping organizational structures, and investing in advanced analytics and technology.
Is it Worth the Investment?
For leading mining companies, the financial potential of improving production predictability is substantial, with gains reaching billions of dollars. Hence, the necessary investment and operational changes are well worth the effort. By addressing the root causes and adopting recommended strategies, companies can improve predictability, reduce revenue losses, and enhance their potential for a successful net-zero transition.
Why Mining Companies Struggle to Meet Production Targets
Several factors contribute to production shortfalls, including gaps in planning and operational challenges, and a variety of external variables. These include geological variability, lower ore quality, unplanned downtime, a shortage of skilled labor, and logistical constraints. By identifying and addressing these root causes, mining companies can reduce revenue shortfalls and work toward meeting their production goals while pursuing sustainability targets. One key planning issue is the insufficient detail in production plans. Improving the granularity of planning and integrating it across all levels of operations can help mitigate performance issues caused by capacity constraints. By adopting a more detailed, data-driven approach to planning, mining companies can improve production outcomes and enhance efficiency. One critical issue in planning is the insufficient resolution or level of detail in the production plan. This can be addressed by implementing more integrated and detailed planning processes. Performance issues related to capacity constraints can also be mitigated through better planning integration across all levels, from the These challenges can be tackled through a targeted, data-driven approach focused on action and analytics.
Data-Driven Strategies for Improving Mining Production
A comprehensive data analysis is the first step in addressing production shortfalls. This includes assessing how well the company’s planning systems align with its operational processes. Companies must examine the integration between information technology (IT) and operational technology (OT), as well as their ability to forecast and manage supply chains effectively. By conducting a forensic analysis, companies can identify root causes and uncover opportunities for improvement. From this analysis, companies can develop a “solution sprint,” a set of actionable steps to address the identified issues. These solutions will include an assessment of the required capital expenditure (capex), the benefits of each initiative, and the necessary resources. Over a 6-10 week period, companies can implement these solutions, making measurable progress within 3-12 months. Successful transformation will require the adoption of new technologies, a shift in organizational mindset, and consistent monitoring of progress.
How Quickly Can Results Be Achieved?
Dr. Elser suggests that by addressing these issues, companies can reduce the typical 2.6% production target miss by 1 to 2% within a year.
Increased Mining Output through Planning and Operations
- Insufficient Planning Detail
More detailed planning and planning integration is essential, from high-level management; “the top-floor” down to the operational “shopfloor”. The mine plan should drive workforce management and enterprise resource planning (ERP) business functions by aligning production, maintenance, and construction processes with broader business functions.A fully connected system enables planning decisions to flow down to individual workers while real-time data and analytics provide feedback to management. This level of visibility ensures that labor shortages and capacity bottlenecks can be proactively addressed, ultimately leading to increased mining production. This so called “Connected Mining Solution”, where the Mine Plan is connected via core ERP functions and Work Force Management & Safety systems, right to the “shop-floor”, is the first step in ensuring a proficient workforce is available to deliver the plan through each milestone.
- Labor Shortages
Workforce efficiency is not just about filling positions; it’s about ensuring proficiency. Recruitment efforts should focus on targeted hiring while automation can supplement gaps in the labor force. Finally ongoing training is required to make the most of your existing workforce. However, success in these areas also depends on a structured training and proficiency validation system that ensures workers have the right skills and capabilities required by the Mine Plan to maximize productivity and increase production output. - Capacity Bottlenecks
Integrated planning and scheduling are critical to avoiding bottlenecks. Implementing AI-driven forecasting tools and improving resource allocation, will help companies anticipate operational constraints before they occur. Having a workforce that is not only present but proficient ensures that constraints are handled efficiently and that production goals are met consistently. - Insufficient Scheduling
Scheduling inefficiencies arise when the workforce management system does not account for proficiency levels at the right time. A proficiency-based workforce system ensures that employees are scheduled based on validated competencies, reducing inefficiencies and downtime and increasing mining production.
Proficiency Over Competency: Building a Workforce That Delivers
A workforce management system focused on proficiency is necessary to ensure that employees not only meet basic competency requirements but also achieve operational excellence. This system should be seamlessly integrated with mine planning, HR recruitment, onboarding, and continuous development programs. Incomplete teams and unverified skill sets account for up to 20% of lost productivity. Instead of simply filling roles, companies must ensure that their workforce has both the required skills and real-world proficiency to execute tasks effectively. Workforce gaps often stem from inadequate visibility into skill levels, leading to teams that lack the required expertise for optimal performance, ultimately reducing mining production potential.
The Financial Impact of Workforce Effectiveness
With the average mine worker earning $125K per annum and 30% additional costs bringing the total to $162K, a 12% productivity loss for a mine with 1,000 workers translates to $19 million per year in lost revenue. Additionally, unnecessary administrative resources due to a lack of automation increase costs by 30%, leading to further inefficiencies and last-minute operational issues. To truly transform operational performance, mining companies need a comprehensive workforce proficiency solution that integrates with mine planning, workforce management, and real-time skill tracking. By focusing on validated skill sets and automation, businesses can eliminate inefficiencies, reduce downtime, and improve overall productivity.
Summary
Problem |
Solution |
Lack of an end-to-end process for managing workforce proficiency | Real-time visibility into workforce skills, training status, and operational readiness |
Incomplete Teams resulting in 12% to 17% productivity loss | Automated systems for managing high-turnover workforces, integrating remote onboarding and skill verification |
Wrong skills or missing competencies and proficiencies causing an additional 10% to 20% productivity loss | A practical assessment framework that validates hands-on proficiency before employees begin their shifts |
The right workforce solution exists. Contact Tutis (hello@tutis.com.au) today to discover how an integrated, proficiency-based workforce management system can help your company close the production gap and drive sustainable profitability. See our next blog for a deep dive into the Connected Mining Solution and how this facilitates planning decisions defining the exact number and nature of the competencies required to execute the mine plan to filter down through HR & recruiting to fill the precise roles, and Onboarding, Mobilization and ongoing to Skills Management and Training to ensure the right people are available at the right time, with the right skills…